Lean Management: Meaning and Advantages
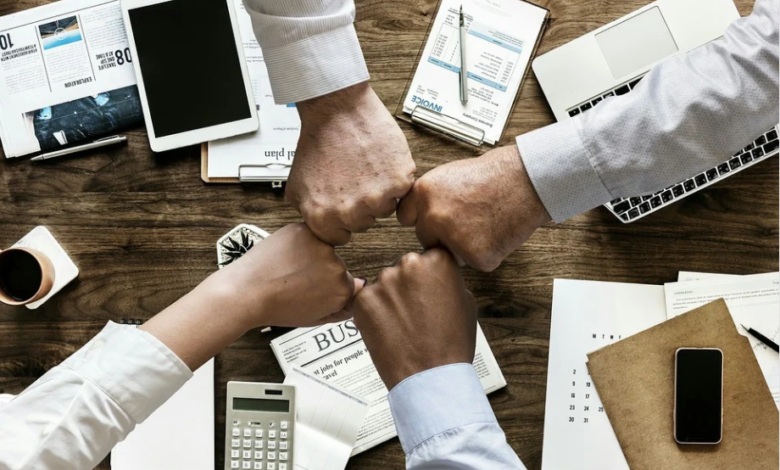
Have you ever thought to start implementing a project, idea or initiative before you fully plan for it? Have you ever implemented a project with an overlap between the planning and implementation stages? Great! You are not alone and somehow you are following the Lean management approach.
Lean management now is one of the most popular concepts in management and industries. It proved its positive impact on companies as a management approach. Simply, lean management approach focuses on managing an organization or business standing on continuous improvement process. We can say that it is a long-term approach aims at improving efficiency and quality through taking small steps and adapting incremental changes.
The Lean management methodologies stands on two main pillars:
- Delivering value from the customers’ or clients’ perspectives.
- Following a continuous improvement strategy.
Eric Ries, an engineer and entrepreneur developed a special methodology to help startups succeed; based on the lean principles. In 2011, he summed up his thoughts in his amazing book called “The Lean Startup”.
The concept stands on 5 principles aim at helping startups to be more flexible and responsive to the dynamic and changeable business environment. The concept works to make the product development cycles short. Also, it works to discover if the given business concept is viable or not.
So, It is not a totally new concept. It has just been more structured and clear. And it should be noted that the Lean Management approach is employed in different sectors such as; government structures, marketing, service or gig economy and others.
Cryptocurrency and Its Evolution
The basic principles of Lean management:
The principles of Lean Management are centered around customer’s needs.
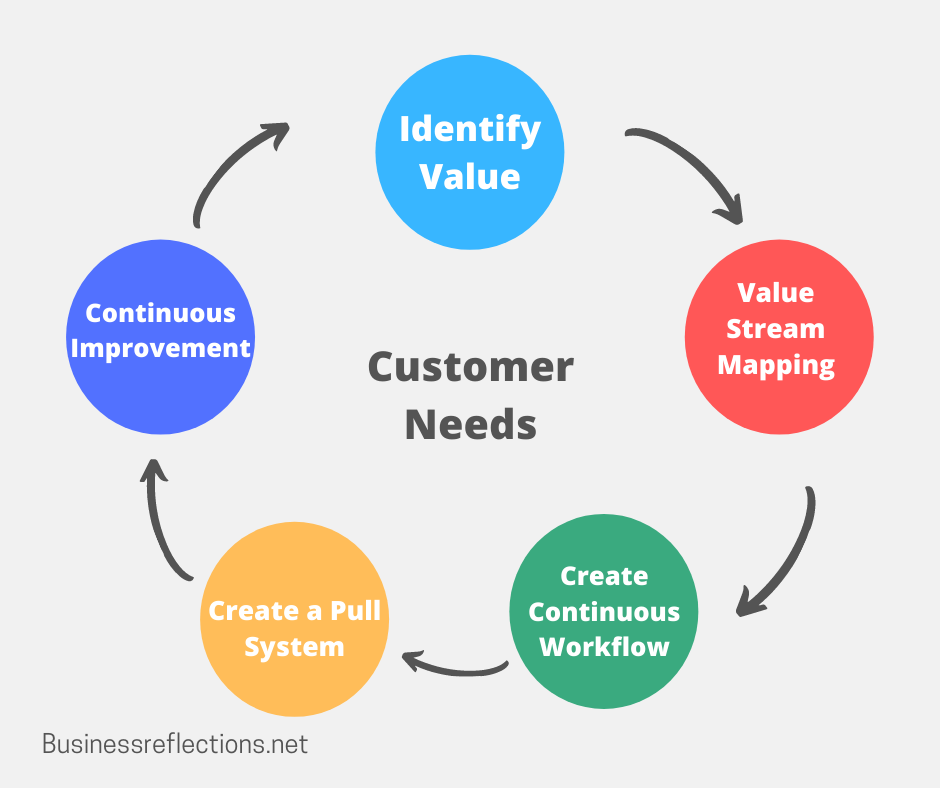
1. Identify Value
Companies are striving to deliver products or services that customers are ready to pay for. So, there is a need to add value and introduce this value to customers through these services or products. But where can we find the value?
Value exists in the problem that customers face and you are trying to solve. It exists in the solution that your customers are willing to find and ready to pay for it. So, it is essential to bring value to your product or service.
2. Value Stream Mapping
Who is responsible for delivering the end service or product to your customers? And what are the required actions to do that?
In this stage, there is a need to map your workflow as a company and identify all actions and parties engaged in delivering the end product to the end users. By doing this, you will be able to identify the useless parts of the process or the less important ones.
By applying the Lean principle in this stage, you will be able to identify where the value of your product or service is being generated so you can make some specific actions such as enhancing or eliminating some parts of work.
3. Create Continuous Workflow
After finishing the mapping of the value stream, there is a need to guarantee that each individual team remains flexible, smooth and adaptable.
Developing your product or service may require cross-functional teamwork and it should be noted that you might face some interruption at any time. However, you can make things easier and remove any roadblock from your track by breaking up the whole work into smaller sub-works and clearing the workflow.
4. Create a Pull System
To ensure that your teams finish tasks much faster and with high quality, you should have a stable workflow. And in order to guarantee a stable workflow, you have to create a pull system. This is how things are done when it comes to lean methodology. What does this mean?
This means that the work is pulled just in case there is a need or demand for it. This step helps you in optimizing your resources and capacity. Also, it helps you to deliver your products or services when there is a real need for them.
5. Continuous Improvement to achieve lean management
After going through all past steps, we can say that you already built your Lean management system. But, you have to pay special attention to this last step.
You have to be aware that problems arise at any time and at any of the previous steps. This means you have to make sure that your employees are engaged in a continuous improvement process at every level.
Different methods and techniques are followed to ensure such kind of improvement. For example, some teams may have a stand-up meeting every day to discuss their agenda, problems and new suggestions.